Understanding Lathe Parts Description: A Comprehensive Guide for Metal Fabricators
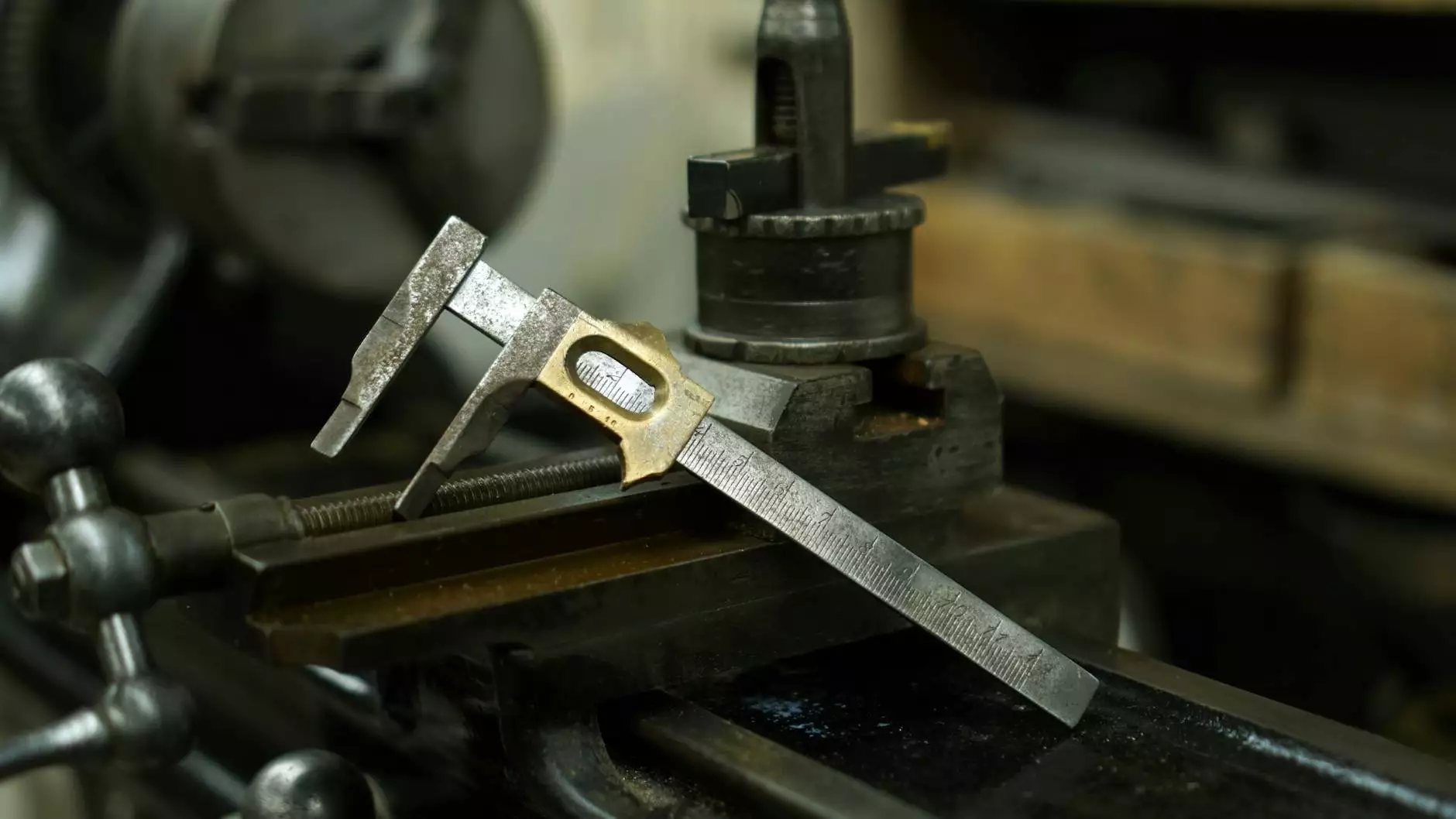
In the world of metal fabrication, the lathe is an indispensable machine tool that plays a pivotal role in manufacturing processes. The precision and accuracy of lathe machine operations hinge on various lathe parts, whose proper description and understanding can significantly impact productivity and quality. This article delves deep into the intricacies of lathe parts description and explores their essential functions in the metal fabrication industry, particularly for businesses like DeepMould.net.
What is a Lathe Machine?
A lathe machine is a tool that rotates a workpiece about an axis to perform various operations such as cutting, shaping, and boring. It is widely used to create cylindrical parts, offering tight tolerances and smooth finishes. Understanding the associated parts of a lathe is crucial for any metal fabricator.
The Importance of Lathe Parts in Metal Fabrication
Lathe parts serve several critical functions in the operation of a lathe machine. Each component plays a unique role that contributes to the overall efficiency and effectiveness of the machining process. The following sections provide a comprehensive lathe parts description.
1. Headstock
The headstock is the powerhouse of the lathe. It houses the main spindle and other key components. In this section, we will explore its functions:
- Main Spindle: Responsible for holding and rotating the workpiece.
- Speed Control: Allows operators to adjust the rotational speed based on the material and operation performed.
- Belt Drive: Transmits power from the motor to the spindle.
2. Tailstock
The tailstock is located opposite the headstock and is crucial for supporting the workpiece during machining. Additionally, it hosts various attachments that enhance functionality:
- Center Support: Provides stability for longer pieces.
- Drilling Capability: Some tailstocks are equipped with a tap or drill chuck for tapping and drilling operations.
- Adjustable Position: Can be moved along the bed to accommodate different workpiece lengths.
3. Bed
The bed is the foundation of the lathe, ensuring stability and alignment for precise operations. Key aspects include:
- Material: Typically made of cast iron or steel for strength.
- Alignment: Must be perfectly straight for accurate machining results.
- Surface Finish: Smooth surface to minimize friction and improve accuracy.
4. Carriage
The carriage moves along the bed and supports the cutting tool. It combines several components:
- Cross Slide: Allows for the lateral movement of the cutting tool.
- Compound Rest: Supports the cutting tool at various angles for tapered cuts.
- Tool Holder: Secures the cutting tool in place.
5. Apron
The apron connects the carriage to the lathe operation controls. Key characteristics include:
- Clutch Mechanism: Engages and disengages the drive for the carriage.
- Feed Controls: Enables precise control of the cutting feed rate.
6. Lead Screw and Feed Rod
These components drive the carriage's movement, providing essential functionality:
- Lead Screw: Utilized for threading operations; it helps the carriage move forward and backward.
- Feed Rod: Provides a simpler feed mechanism for cutting operations.
Common Lathe Parts Description: Understanding Their Impact on Operations
When describing lathe parts, it's imperative to understand how they interact with one another and their collective impact on machining operations. A comprehensive lathe parts description helps operators make informed decisions, leading to improved quality and efficiency in production.
7. Tool Post and Tool Holder
The tool post secures the cutting tool in the correct position. The tool holder allows quick changes of tools for different operations:
- Quick Change Tool Post: Enables rapid tool changeovers.
- Adjustability: Tool holders can be adjusted to achieve the desired depth and angle.
8. Chucks
Chucks are essential for holding the workpiece securely. There are various types:
- Three-Jaw Chuck: Provides concentric grip on cylindrical parts.
- Four-Jaw Chuck: Offers greater flexibility in holding irregular shapes.
- Collet Chuck: Best for precision work on small parts.
9. Tailstock Taper and Morse Taper
The tailstock taper serves as the interface for supporting tools such as drills:
- Morse Taper: A common system used for tapering tools for easy insertion and removal.
- Adjustable Tailstock: Ability to adjust the height and position of tooling.
Enhancing Your Metal Fabrication Business with Quality Lathe Parts
For metal fabricators like those at DeepMould.net, understanding the lathe parts description allows for more informed procurement decisions. Choosing high-quality components can significantly enhance operational efficiency and product quality. Here are some tips to improve your lathe operations:
1. Invest in Quality Parts
Always opt for high-quality lathe parts. Inferior parts can lead to frequent breakdowns, hinder productivity, and negatively impact product quality.
2. Regular Maintenance and Inspection
Implement a routine inspection and maintenance schedule. Regular checks can prevent malfunctions and extend the lifespan of your lathe machine.
3. Continuous Training for Operators
Provide your operators with ongoing training on the latest techniques and technologies. A well-trained workforce can efficiently handle complex operations and troubleshoot issues as they arise.
4. Documentation of Lathe Parts Description
Maintain comprehensive documentation for all lathe parts descriptions. This includes specifications, maintenance history, and operational guidelines to streamline processes and improve efficiency.
The Future of Metal Fabrication and Lathe Operations
As technology advances, the future of metal fabrication will certainly involve enhanced lathe mechanisms and parts. Innovations may include:
- Smart Lathe Technology: Integration of IoT for real-time monitoring and remote control.
- Advanced Materials: Development of lightweight yet durable materials for lathe components.
- Automation: Increased automation for precision, consistency, and efficiency.
Conclusion: Mastering Lathe Parts Description for Industry Success
In conclusion, mastery of lathe parts description is essential for successful operations in the metal fabrication industry. Understanding the individual and collective functions of each component enables businesses like DeepMould.net to optimize their machining processes, reduce downtime, and produce high-quality outputs. By investing in quality parts, implementing best practices, and staying abreast of industry innovations, you can secure a competitive edge in the ever-evolving landscape of metal fabrication.
Empower your metal fabrication business by fully embracing the potential of your lathe machine through comprehensive understanding and strategic investments in lathe parts.