Precision Injection Molding Manufacturers: A Comprehensive Guide
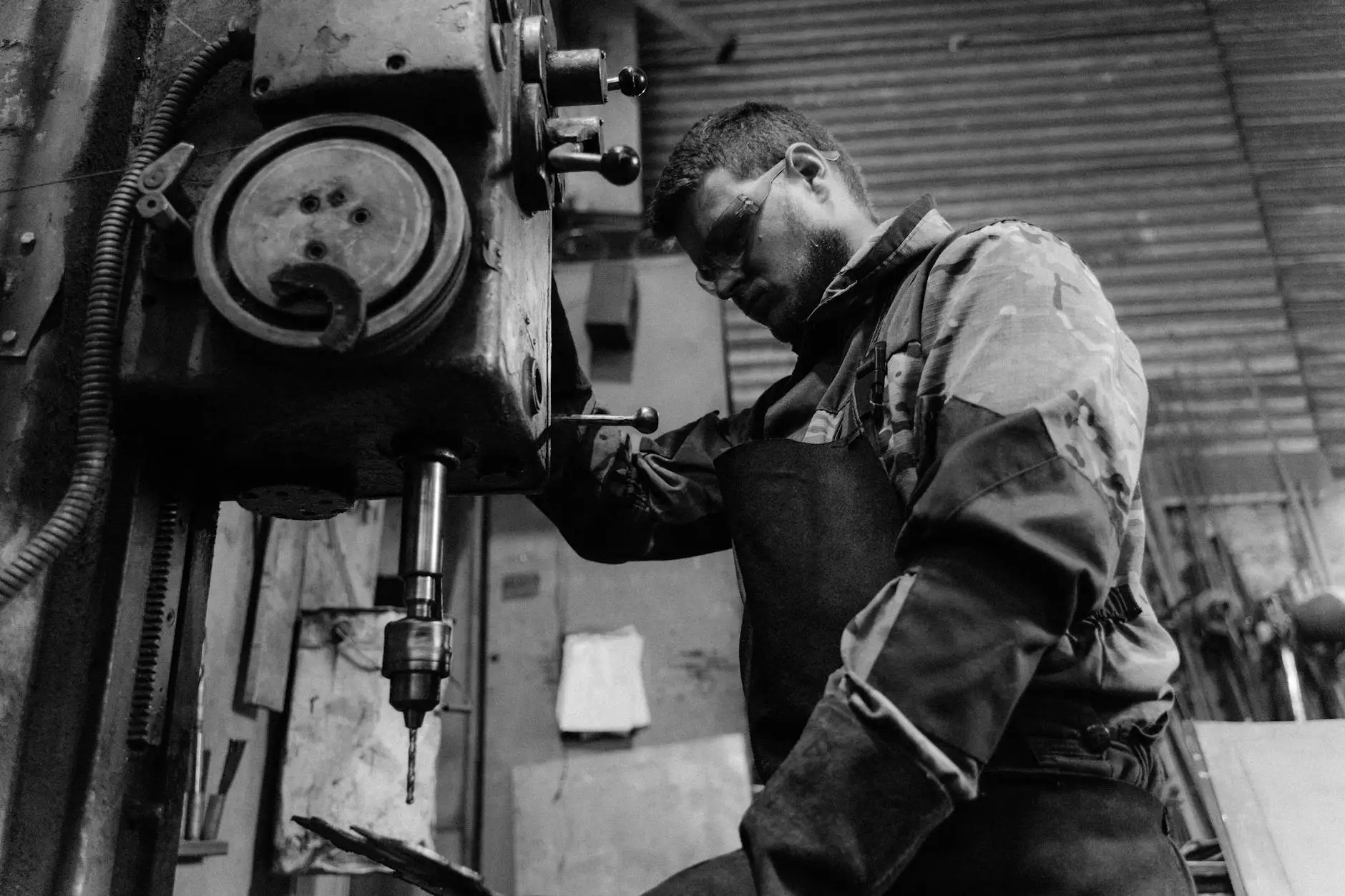
In today’s fast-paced industrial landscape, the role of precision injection molding manufacturers cannot be understated. Their contributions to the manufacturing sector enable businesses to produce high-quality components efficiently and cost-effectively. This article delves into the intricacies of precision injection molding, the process involved, and how these manufacturers can elevate a business’s production capabilities.
Understanding Precision Injection Molding
Injection molding is a manufacturing process used for producing parts by injecting material into a mold. It’s particularly favored for producing high volumes of parts with consistent quality. When we refer to precision injection molding, we highlight a refined version of this technique that prioritizes tight tolerances and complex geometries often required in industries such as automotive, medical devices, and consumer electronics.
The Importance of Precision in Manufacturing
Precision in manufacturing processes like injection molding affords several significant benefits:
- Consistency: Precision ensures that every product meets specified tolerances, reducing defects and wastage.
- Efficiency: High precision can lead to faster production times and lower costs per part.
- Complexity Handling: Precision molding allows for intricate designs that might be unfeasible with traditional processes.
How Precision Injection Molding Works
The process of precision injection molding can be broken down into several detailed steps:
- Mold Design: The first step involves creating a mold that has been precisely designed to meet the specifications of the parts being produced.
- Material Selection: Choosing the right material is crucial as it will affect the durability and functionality of the final product.
- Injection: The chosen material is heated until it becomes liquid and then injected into the mold under high pressure.
- Cooling: Once the material fills the mold, it cools and solidifies to take on the shape of the mold.
- Demolding: The finished product is ejected from the mold, and any finishing processes are applied.
Key Factors Contributing to Precision
To achieve optimal precision, several factors need to be meticulously managed:
- Mold Material: High-quality steel or aluminum improves durability and precision.
- Temperature Control: Consistent heating and cooling temperatures are vital for preventing warping or defects.
- Injection Speed: Controlling the speed at which the material is injected helps ensure that it fills the mold evenly.
- Quality Assurance: Regular checks and adjustments during the manufacturing process safeguard against defects.
Applications of Precision Injection Molding
The applications of precision injection molding are extensive and span multiple industries:
1. Automotive Industry
The automotive sector utilizes precision molded parts for various components such as dashboards, engine parts, and electrical housings. The high level of precision ensures safety, functionality, and aesthetic quality.
2. Medical Devices
In the medical field, precision is critical. Components used in medical devices, from surgical instruments to diagnostic equipment, must meet stringent safety standards, which precision injection molding can reliably provide.
3. Consumer Electronics
The consumer electronics sector relies on precise molds for manufacturing parts like casing for smartphones, tablets, and other devices, where aesthetics and functionality are paramount.
4. Industrial Equipment
Manufacturers of industrial equipment utilize precision molding for producing robust components that can withstand harsh conditions while maintaining operational integrity.
Choosing the Right Precision Injection Molding Manufacturer
When it comes to selecting a precision injection molding manufacturer, several factors come into play:
- Experience: Look for manufacturers with a proven track record in precision injection molding.
- Technology: State-of-the-art machinery often results in higher quality parts.
- Customization Capabilities: A good manufacturer should be able to tailor their services to meet unique business needs.
- Quality Control: Ask about their quality assurance processes and certifications to guarantee the highest standards.
- Customer Service: Good communication and support are critical for addressing issues that may arise.
Advantages of Working with Precision Injection Molding Manufacturers
Partnering with established precision injection molding manufacturers such as Deep Mould offers numerous advantages:
1. Cost-Effectiveness
By producing large quantities of parts with minimal waste, precision injection molding significantly reduces manufacturing costs.
2. Scalability
Manufacturers can easily scale production up or down based on demand, allowing businesses to respond swiftly to market changes.
3. Enhanced Quality
Consistent quality achieved through precision processes leads to increased customer satisfaction and reduced return rates.
4. Speed to Market
Precision injection molding facilitates faster prototype production, allowing companies to bring their products to market quicker.
Conclusion: The Future of Precision Injection Molding
As industries continue to evolve, the role of precision injection molding manufacturers will become even more integral. With advancements in technology, such as automation and smart manufacturing, the potential for greater efficiency and enhanced quality is promising. Businesses are encouraged to explore partnerships with skilled manufacturers to leverage the advantages of precision injection molding for their production needs, ensuring they remain competitive in a rapidly changing market.
Investing in precision injection molding is not merely adopting a manufacturing process; it is embracing a transformative approach to production that can redefine efficiency, quality, and innovation within any business sector. As you consider your options, remember the pivotal role these manufacturers play in facilitating your success.