Understanding Plastic Prototype Manufacturing
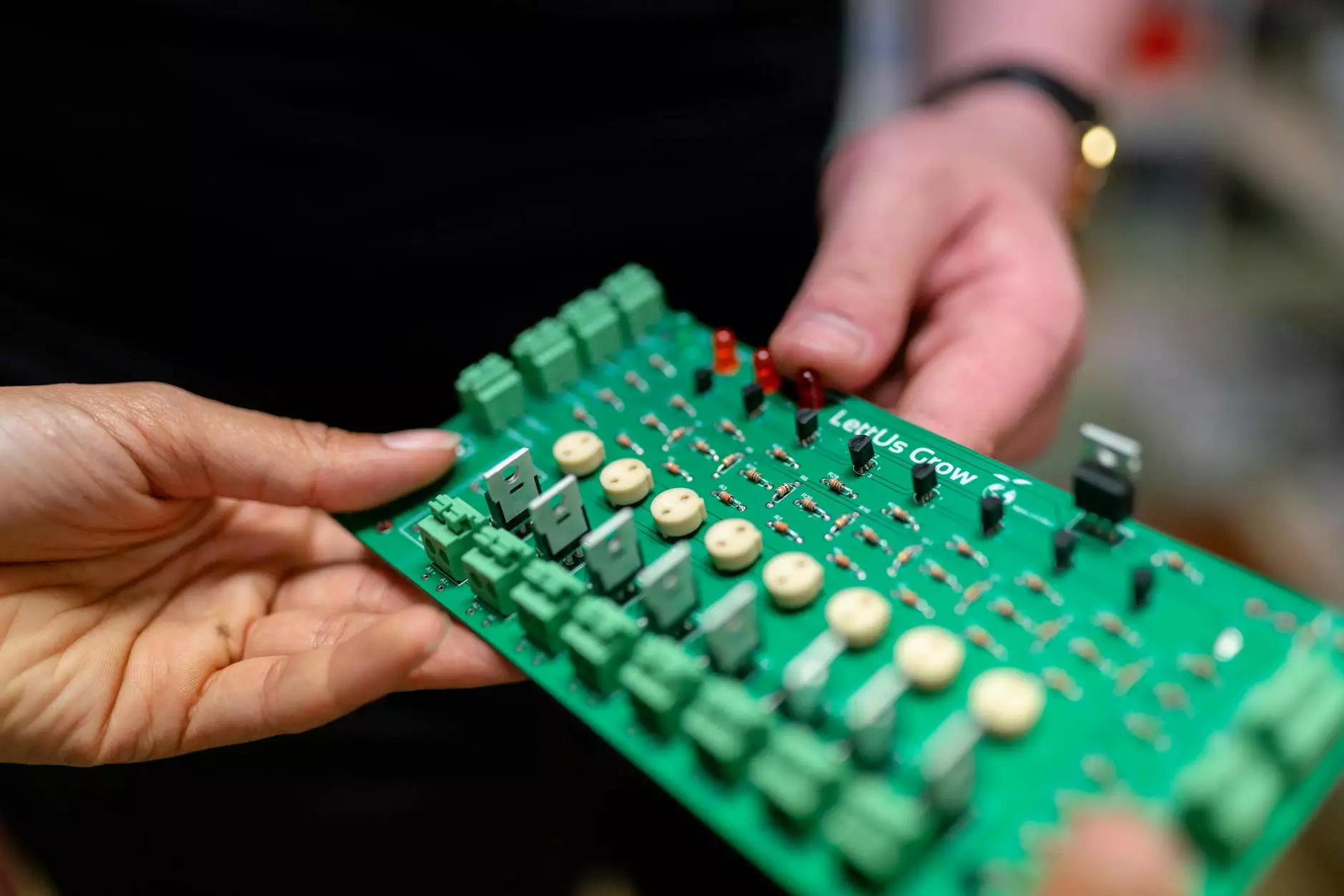
Plastic prototype manufacturing plays a crucial role in modern product development. In an era where innovation is key, organizations seek efficient ways to turn concepts into tangible products swiftly. This article explores the depths of plastic prototype manufacturing, discussing its significance, processes, advantages, and its interrelation with metal fabrication, thereby providing you with a comprehensive understanding of this vital industry.
The Importance of Plastic Prototyping
Plastic prototypes are essential for verifying design concepts, saving time and costs, and enhancing innovation. They allow companies to:
- Visualize Products: Transform abstract ideas into concrete representations.
- Test Functionality: Evaluate how a product will perform in real-world scenarios before mass production.
- Identify Flaws Early: Detect design flaws early in the development stage, reducing the cost of changes later.
- Gather Feedback: Obtain feedback from stakeholders and users to refine the design.
Techniques in Plastic Prototype Manufacturing
Various techniques can be employed in plastic prototype manufacturing. Each has unique advantages suited to different project requirements:
1. 3D Printing
3D printing has revolutionized plastic prototyping by allowing for rapid production of complex shapes that may be difficult to achieve with traditional methods. Common technologies include:
- Fused Deposition Modeling (FDM): Utilizes thermoplastic filament to build prototypes layer by layer.
- Stereolithography (SLA): Employs UV light to cure resin into hardened plastic, producing high-resolution parts.
- Selective Laser Sintering (SLS): Uses lasers to fuse powdered plastic into solid structures.
2. CNC Machining
CNC machining offers unparalleled precision in prototype manufacturing. It is ideal for creating durable and functional prototype parts from solid plastic blocks. The process includes:
- Designing the CAD Model: Creating a digital representation of the intended prototype.
- Programming the CNC Machine: Setting the machine with the correct parameters to carve the material accurately.
- Production: The CNC machine processes the plastic into the final prototype form.
3. Injection Molding
Injection molding is a preferred method for mass-producing prototypes that require durability. This process involves:
- Creating the Mold: Designing a mold that reflects the desired prototype shape.
- Injection of Molten Plastic: Heating plastic granules and injecting them into the mold under high pressure.
- Curing and Finishing: Allowing the plastic to cool and harden before removing it from the mold.
Advantages of Plastic Prototype Manufacturing
The benefits of utilizing plastic prototype manufacturing in product development are extensive:
- Cost Efficiency: By identifying design issues early, companies can save on prototype revisions and production costs.
- Speed to Market: Rapid prototyping methods allow businesses to bring products to market faster than their competitors.
- Design Flexibility: Plastic prototypes can be easily modified compared to fixed materials, fostering a culture of innovation.
- Enhanced Communication: Physical prototypes serve as effective communication tools between stakeholders, designers, and manufacturers.
The Intersection of Plastic Prototype Manufacturing and Metal Fabrication
At DeepMould.net, we recognize that successful product development often involves a marriage of plastic prototype manufacturing and metal fabrication. Understanding this intersection allows businesses to:
- Optimize Design: Combine the benefits of plastics and metals to produce hybrid solutions that meet specific product requirements.
- Streamline Production: Reduce the need for complex assembly by integrating both fabrication methods into a single manufacturing process.
- Improve Performance: Use metals for strength and plastics for weight reduction, leading to enhanced performance and functionality.
Challenges in Plastic Prototype Manufacturing
While the advantages are significant, there are challenges in plastic prototype manufacturing that businesses must navigate:
- Material Selection: The choice of plastic can affect the prototype’s performance, durability, and aesthetics.
- Cost Management: Balancing quality with cost when producing prototypes can be challenging, especially in small batches.
- Technical Expertise: There is a growing need for skilled professionals to operate advanced manufacturing technologies and refine the design process.
Future Trends in Plastic Prototype Manufacturing
As technology advances, the field of plastic prototype manufacturing is evolving. Here are some trends to watch:
- Increased Automation: The rise of automation in manufacturing processes is leading to greater efficiency and reduced human error.
- Biodegradable Materials: The demand for sustainable materials is pushing manufacturers to explore eco-friendly options.
- Integration of AI: Artificial Intelligence is expected to play a key role in design optimization and predictive maintenance of manufacturing equipment.
Conclusion
In conclusion, plastic prototype manufacturing is an indispensable part of product development that significantly enhances the design and manufacturing process. The techniques, advantages, and future trends discussed in this article demonstrate the critical role that effective prototyping plays in innovation and market success. At DeepMould.net, we are committed to providing top-notch solutions in both plastic and metal fabrication, ensuring that our clients can bring their visions to life efficiently and effectively.
Explore how our expertise in plastic prototype manufacturing can transform your product development journey. Contact us today to discover more!