Understanding the General Tolerance Chart for Plastic Parts in Metal Fabrication
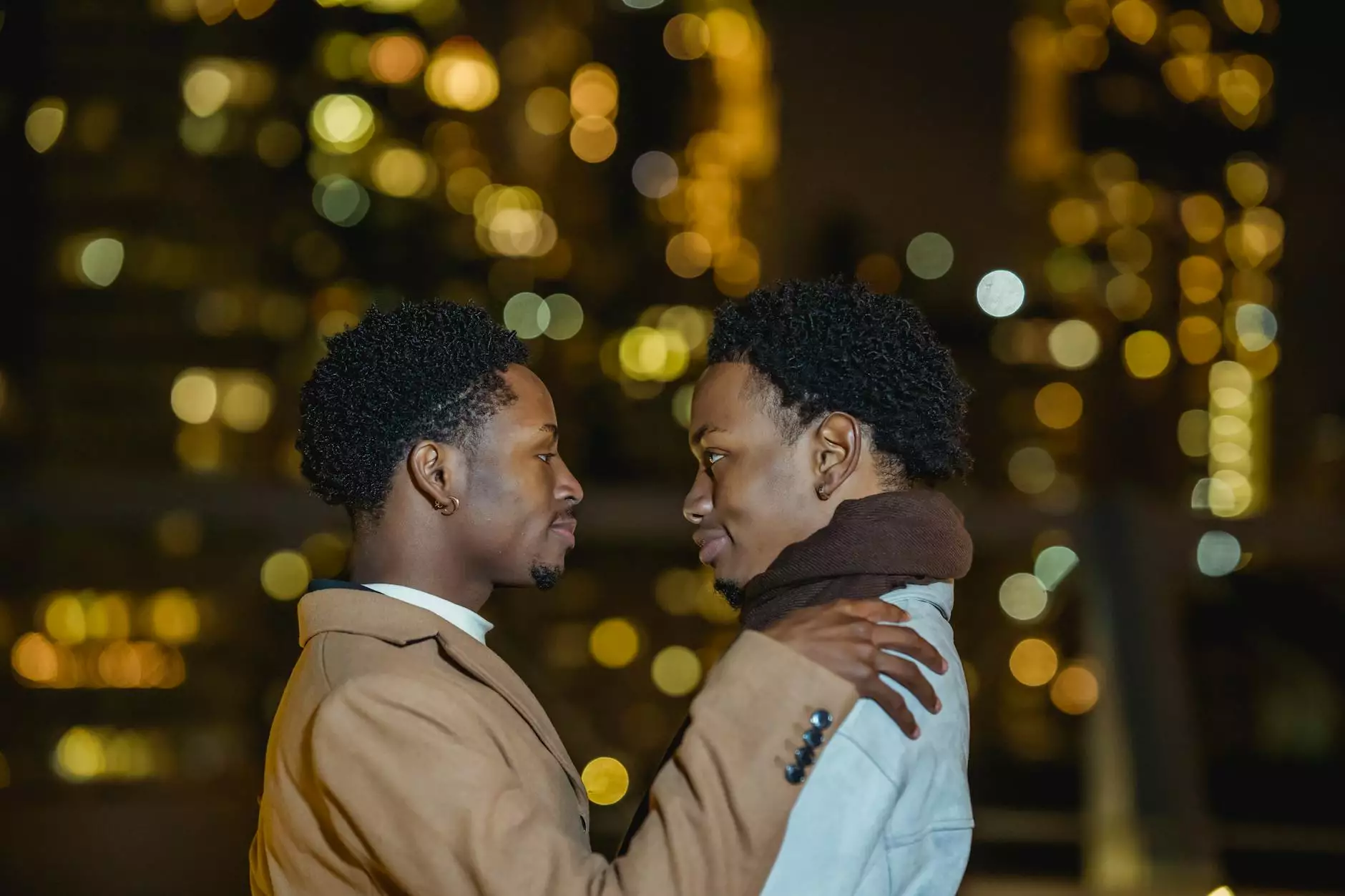
The world of metal fabrication is intricately linked with the engineering and design of plastic parts, making the general tolerance chart for plastic parts an essential tool in ensuring the precision and quality desired in manufacturing. In this article, we will explore the significance of tolerance charts, their applications, and best practices that lead to successful outcomes in the production process.
What Is a General Tolerance Chart?
A general tolerance chart serves as a guideline for acceptable deviations in dimensions when producing parts, specifically plastic components in our case. These tolerances are critical for ensuring that manufactured parts fit together correctly and function as intended. The chart specifies the permissible limits of variation for various features, allowing manufacturers to design intricate parts with confidence.
Why Tolerance Matters in Manufacturing
- Precision: Tolerance assures that components fit seamlessly, reducing assembly issues.
- Quality Control: It helps in maintaining quality standards across batches of products.
- Cost-Effectiveness: Adhering to tolerance guidelines can minimize material waste and rework costs.
- Safety: In applications where safety is critical, such as automotive or aerospace, proper tolerances can avoid catastrophic failures.
Key Components of a General Tolerance Chart
Understanding the components of the general tolerance chart for plastic parts is essential for effective application. Below are some key elements commonly included in these charts:
1. Dimensions
Each feature of a part is measured and defined by its dimensions, such as length, width, and diameter. The chart specifies the nominal size along with the acceptable tolerances.
2. Tolerance Values
Tolerances may be expressed as a range (e.g., ±0.05 mm) or as a total tolerance value. These specifications guide manufacturers on how much deviation is allowed from the nominal dimensions.
3. Feature Types
Different types of features (e.g., holes, slots, curves) may have distinct tolerances due to their functional purposes. The chart provides insights into what tolerances are applicable for different feature types.
4. Material Implications
The chart also takes into consideration the type of material being used. As plastic parts behave differently from metals, adjustments in tolerance might be necessary based on the material properties.
Applications of Tolerance Charts in the Plastic Manufacturing Industry
The utilization of tolerance charts is widespread within the industry, particularly in sectors where plastic parts are integral. Here are significant applications:
Precision Engineering
In precision engineering, adherence to specific tolerances is vital. Tolerance charts enable engineers to design complex assemblies where every component must fit together perfectly, contributing to the overall functionality and longevity of the product.
Automotive Industry
In automotive manufacturing, the precision of plastic components is paramount. Cars incorporate a myriad of plastic parts, from dashboards to engine casing. Using the general tolerance chart for plastic parts ensures that all components operate efficiently together, ensuring safety and performance.
Aerospace Applications
The aerospace sector demands the highest degree of tolerances due to the criticality of component failure. Parts are often subjected to extreme conditions, and thus, the tolerance chart becomes a fundamental resource for engineers in design and manufacturing phases.
Best Practices for Utilizing Tolerance Charts
To maximize the benefits derived from the general tolerance chart for plastic parts, various best practices should be adhered to:
1. Collaboration Between Design and Manufacturing Teams
Ensuring that design and manufacturing teams collaborate effectively is crucial. Tolerance specifications should align with manufacturing capabilities, thereby preventing issues arising from mismatched expectations.
2. Regular Updates and Reviews
As manufacturing technologies evolve, regularly updating tolerance charts to reflect new capabilities and insights is essential. Regular reviews ensure that the chart remains relevant and applicable.
3. Training and Skill Development
Providing training for staff on understanding and utilizing tolerance charts will lead to better comprehension and application in daily operations, enhancing overall product quality.
4. Feedback Mechanisms
Implementing effective feedback mechanisms allows for monitoring the performance related to component tolerances. Insights gained can lead to iterative improvements in the manufacturing process and tolerance specifications.
Conclusion
In summary, the general tolerance chart for plastic parts is an indispensable tool in the world of metal fabrication and beyond. As industries increasingly depend on precise and high-quality plastic components, understanding and effectively utilizing these charts will pave the way for enhanced quality, performance, and cost-efficiency in manufacturing processes. By applying the best practices outlined in this article, businesses can ensure they stay competitive and deliver excellence in their operations.
Final Thoughts
By embracing the principles of tolerance and manufacturing best practices, companies in the metal fabrication industry, particularly those involved with plastic parts, can achieve exemplary operational standards. Relying on detailed and comprehensive resources such as the general tolerance chart for plastic parts allows manufacturers to gauge their performance and strive for continuous improvement, ultimately benefiting both the company and the customer alike.