Advantages of Electric Injection Molding for Metal Fabricators
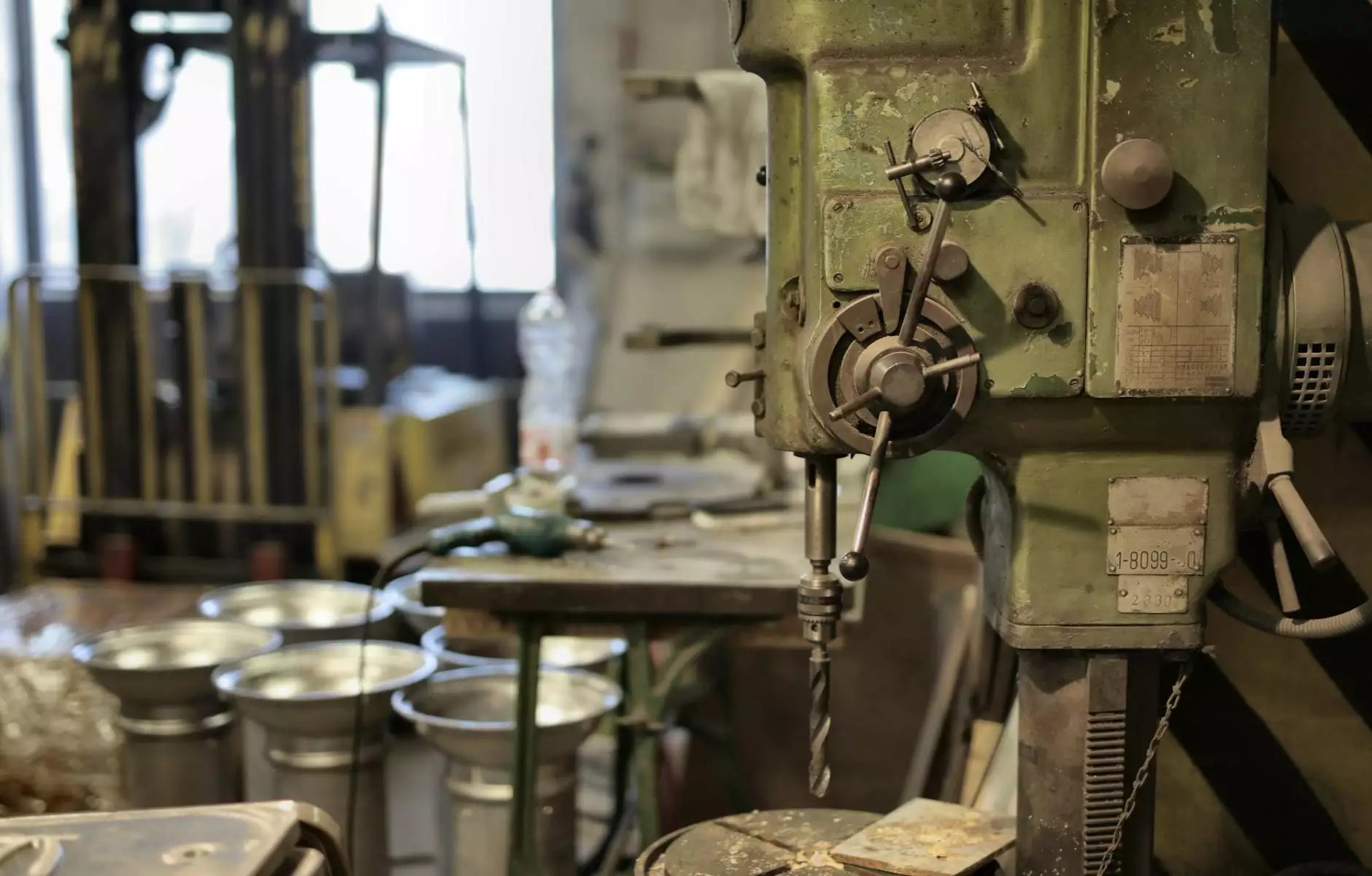
Introduction
As technology continues to reshape the manufacturing industry, electric injection molding has emerged as a game-changer for metal fabricators. This innovative process offers numerous benefits, including enhanced efficiency, precision, and cost-effectiveness. In this article, we will delve deeper into the advantages of electric injection molding and how it can revolutionize the metal fabrication industry.
Understanding Electric Injection Molding
Electric injection molding is a highly advanced manufacturing technique that involves injecting molten metal into a precision mold. Unlike traditional methods, which rely on hydraulic or mechanical systems, electric injection molding utilizes electric servo motors to control the molding process. This level of precision and control enables metal fabricators to produce complex parts with utmost accuracy and repeatability.
The Advantages
Electric injection molding offers a range of advantages that significantly enhance the overall metal fabrication process. Let's explore these advantages in detail:
1. Enhanced Efficiency
Electric injection molding machines are designed to optimize energy consumption, making them more efficient compared to their hydraulic counterparts. The precise control offered by electric servo motors enables quick and accurate movements, reducing cycle times and increasing overall productivity. This enhanced efficiency translates into faster turnaround times and increased capacity for metal fabricators.
2. Improved Precision
One of the primary advantages of electric injection molding is its ability to achieve exceptional precision. The precise control over speed, pressure, and position of the mold translates into consistent and accurate part production. This level of precision is vital in industries where even the smallest deviation can lead to product failure or performance issues. Metal fabricators can rely on electric injection molding to consistently produce high-quality, dimensionally accurate parts.
3. Cost-Effectiveness
While electric injection molding may have a higher upfront cost compared to hydraulic systems, its long-term cost-effectiveness is undeniable. The energy efficiency of electric servo motors leads to significant energy savings, reducing operating costs over time. Additionally, the precise control and repeatability of electric injection molding minimize material waste and rework, further reducing costs for metal fabricators.
4. Environmentally Friendly
Electric injection molding is a greener alternative to traditional molding methods. By utilizing electric servo motors, the process minimizes the reliance on hydraulic fluids, which are often associated with environmental concerns. The energy efficiency aspect also contributes to a reduced carbon footprint, making electric injection molding an environmentally friendly choice for metal fabricators who prioritize sustainability.
Conclusion
In conclusion, electric injection molding has revolutionized the metal fabrication industry by offering enhanced efficiency, improved precision, cost-effectiveness, and eco-friendliness. Metal fabricators who adopt this advanced technology can gain a competitive edge in the market, achieving higher productivity, superior product quality, and overall customer satisfaction. Experience the advantages of electric injection molding for your metal fabrication needs at DeepMould.net and take your business to new heights.